Smart Manufacturing with Cobots: Castec’s i-Operator Mobile Robots
Castec’s i-Operator Mobile Robots stands out as a remarkable innovation by offering a blend of advanced functionality and human-like adaptability. Partnering up with OMRON and Universal Robots (UR), Castec has created a dynamic mobile cobot solution that can be easily applied in a range of use cases. In this issue of Automation In Focus, we will be spotlighting AutomationSG member Castec.
The i-Operator’s ability to navigate autonomously without the need for guiding tracks, dynamically plan paths, and re-route when obstacles arise showcases an exceptional level of sophistication that sets it apart from other mobile robots. Its comprehensive safety features—ranging from E84 standards to multi-directional laser sensors—ensure a safe and efficient material handling process, making it particularly well-suited for the demanding requirements of semiconductor manufacturing.
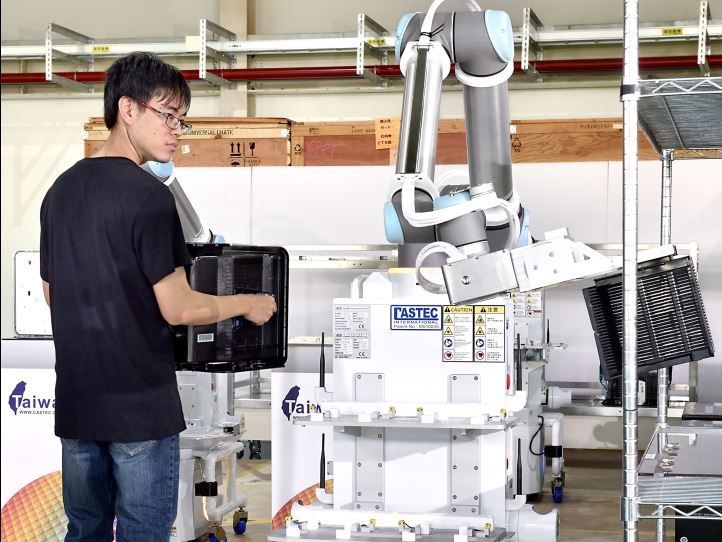
Besides its impressive capabilities, the i-Operator exemplifies how automation can seamlessly integrate cutting-edge robotics with practical, real-world applications to address industry-specific challenges. Its emphasis on safety, efficiency, and connectivity highlights the possibilities of creating smarter, more adaptive manufacturing environments. We interviewed Castec to find out more about what goes behind their innovative design.
What inspired Castec to come up with the design of the i-Operator mobile robot?
It is increasingly difficult to find workforce for mundane jobs in manufacturing sector due to many factors, such as aging population, higher education level, government regulations, etc. With the emergence of autonomous mobile robot and collaborative robot arm, Castec came out with the concept of integrating these two to build a human-size robot, i-Operator, which helps to execute those simple and repetitive jobs, by imitating how a human works.
How does the i-Operator stand out from other smart mobile robots?
In semiconductor manufacturing, production floor space is very precious and costly. Aisles are narrow, typically 1.2m or less. Bigger robots will have difficulties maneuvering around. i-Operator is designed to be a human-size which is able to work hand-in-hand with human operator. Due to its smaller size, the human operator would not feel intimidated. Its design is also carefully thought through to ensure safety of human, products, equipment, production environment, and the robot itself.
What are some of the interesting use cases of the i-Operator?
Other than production use, i-Operator has also been used to welcome foreign country’s VIP by waving flags to them and deliver golden scissors to VIP for opening ceremony use.
How does the i-Operator enhance efficiency in manufacturing processes?
Typically, due to precision need, a robot is designed to handle only one type of material. However, in many manufacturing processes, there is more than one type of material to be handled. Instead of having multiple robot designs to handle different material types, i-Operator is designed to handle more material types as far as possible to enhance efficiency. i-Operator will also maximize its storage space’s design. In addition, i-Operator’s system will intelligently determine the best sequence and route to handle the materials. This reduces the number of travelling trips and maximizes the output of every trip it makes.
With its advanced safety detection systems, how does the i-Operator ensure a safe environment for operators and precision while handling the materials?
i-Operator uses multiple types of safety sensors, including laser sensors, sonar sensors, presence sensors, etc. These are the preventive measures. It also adopts “if everything fails” measure such as collision sensor to ensure no damage or injury during its operation. Just like standard equipment, there are also easily accessible EMO emergency buttons as a last resort. One of the benefits of using robots is its repeatability and precision. If this does not work well, not only that it doesn’t help production, it will be a burden to the production. i-Operator adopts a 2-tier alignment method and uses a high-resolution CCD camera to achieve the required precision in handling of materials.
How does the i-Operator integrate with the existing workflows as a cobot?
i-Operator working behaviour is similar to a line operator. It receives instructions based on the process flow and executes them accordingly. The key difference is that while line operator refers to instructions either on paper or on monitor screen, the instructions for robot is in the background, making production floor looks neater.
How were the partnerships with OMRON and Universal Robot (UR) instrumental in developing the i-Operator?
Omron and Universal Robot are both well-established products. This reduces our effort to verify their safety and stability. It makes integrating them into i-Operator a breeze.
How do you envision mobile robots evolving in the upcoming years?
i-Operator is a semi-humanoid robot used in manufacturing. Humanoid robots are evolving. They would be more nimble and versatile. Together with AI development, humanoid robots could be the main production workers in manufacturing, relieving the manpower to more value-added jobs.
What are some other use cases you wish to see the i-Operator implemented in future?
i-Operator is currently used mainly in semiconductor industry. This benefitted roughly 35,000 people working in Singapore semicondcutor industry, by relieving them from the dull repetitive work. There are other sectors in Singapore which are also facing difficulties in hiring, eg. Healthcare, hospitality, food. I hope i-Operator would be able to provide a solution for them.